We love getting deeper into what we do and sharing our findings with you. So we’ve teamed up with our R&D team to start a new blog series called “The Science of” where we explain things from a technical perspective. We hope you enjoy these unadulterated content by our R&D team!
What are ceramic coatings?
Ceramic coatings, also commonly known as glass coatings, nano coatings, silica coatings and hydrophobic coatings, are defined as a semi-permanent, non-metallic, inorganic protective clear coat, that is applied on several type of different surfaces. Ceramic coatings are utilized in different industries such as automotive, marine and architecture, primarily for its easy-to clean properties and protection against weathering.
The basic formulation of any ceramic coating includes:
- resin (polymeric material that build-up the backbone of coating);
- solvent(s); and
- additives.
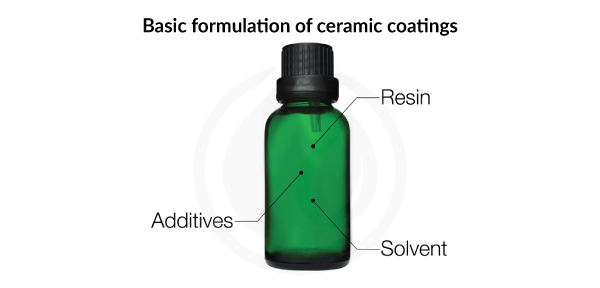
Resin is one of the key components of a ceramic coating system. Common resins include silicone-based polymers such polydimethylsiloxanes (PDMS). PDMS are commonly used in the formulation of ceramic coatings as it is generally non-toxic, inert, non-flammable, optically clear with excellent thermal and is UV stable.
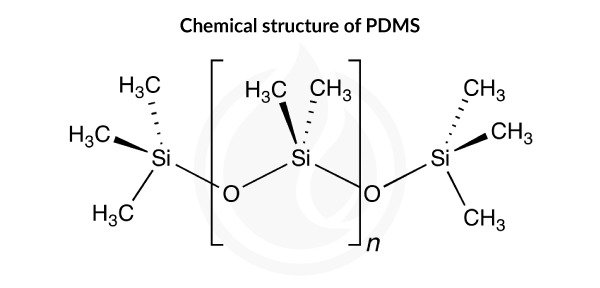
PDMS is usually employed as the main component in a ceramic coating system which provides the hard, glossy and hydrophobic characteristics. The structure and formation of a PDMS based ceramic coating is illustrated below.
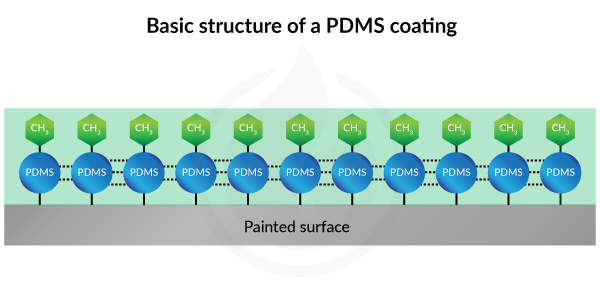
Unfortunately, PDMS on its own has poor adhesion to paints, plastic, metal and wood substrates. With the addition of silane additives to the formulation to promote adhesion, PDMS is able to create a linkage between PDMS and the substrate to form a semi-permanent thin protective film, as displayed below.
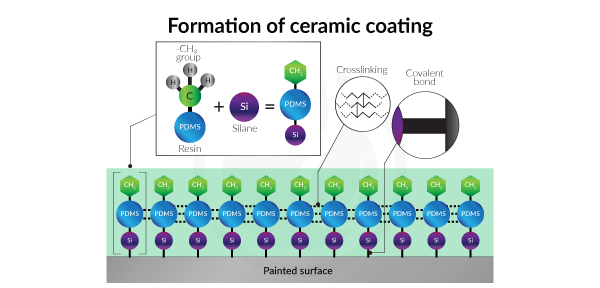
The silane functional group (-Si-O-R) reacts with the surface to form a strong covalent bond, which contributes to the improvement of overall coating adhesion and helps to improve the durability of the ceramic coating, especially when subjected to mechanical abrasion such as washing and rubbing.
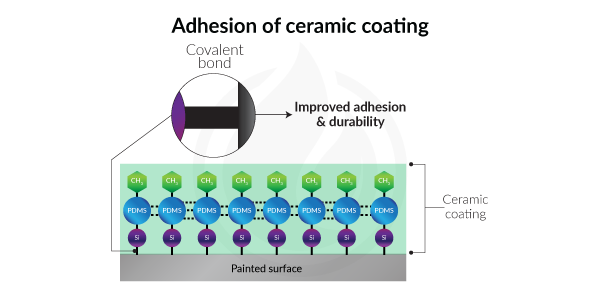
How does PDMS form a protective coating with its particular characteristics like its hardness, hydrophobicity and resistance to chemicals?
PDMS begins to cure when it comes in contact with moisture in the air. The curing process takes a long time and is typically accelerated with the presence of catalysts. Usually, the ceramic coating is dry-to-touch within hours but the full curing process usually takes between 5 to 7 days. As the PDMS begins to hydrolyze, each PDMS monomer will bind together to form a longer chain, resulting in a thin but rigid protective layer on the surface. The hydrolysis reaction is shown below.
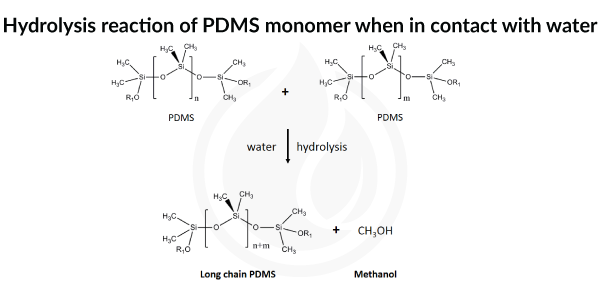
Throughout the hydrolysis reaction, methanol (or any other alcohols compound) will be emitted as a by-product of the reaction, depending on the grade of the PDMS used. This byproduct is commonly known as volatile organic compounds or VOC. While most coatings in the industry are “strong smelling”, the coatings formulated by IGL Coatings are low or have zero VOCs, which means less emissions of VOC by-products during curing.
The hardness of the PDMS-based ceramic coating is dependent on the crosslinking agents in the formula. Without the addition of the crosslinking agent into the ceramic coating system, the monomer of the PDMS will tend to react along the main chain, forming a longer chain with minimal crosslinking. This results in coatings with moderate hardness. This type of coating system is commonly available in the market as 1-component (1-K) products with a longer pot-life.
Note: Pot-life means the time window where the mixture is still suitable for use.
When a crosslinking agent is introduced, the intermolecular bonds between adjacent PDMS chains are formed, as displayed below.
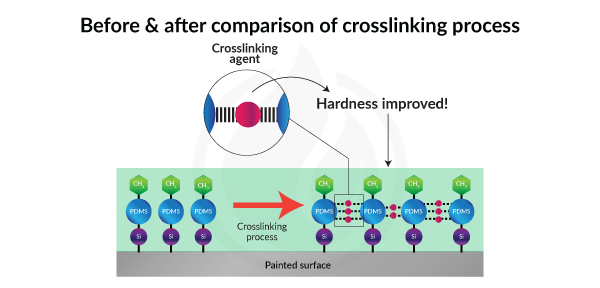
This results in a ceramic coating with higher crosslink density, producing ceramic coatings with pencil hardness rating of up to 10H such as IGL Coatings ecocoat KENZO.
However, the pot-life of the PDMS with crosslinking agent is very limited (few hours to 1 days). Therefore, the formulator is required to formulate a coating with two separate components (2-K) (such as ecocoat window) to prevent pre-mature reaction during storage. 2-K products require the end-user to mix the two components.
The hydrophobicity of the PDMS-based ceramic coating is formed during the curing process when the -Si-O-Si- bond is formed.
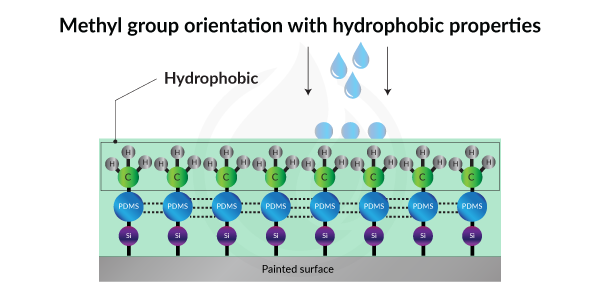
In this process of curing, the methyl groups would be orientated in such a way that it would be aligned facing to the coating surface as shown below, resulting in superior hydrophobic/water repellent property. Depending on the formulation of the ceramic coating, the water contact angle differs between 91° to 120°.
Due to the hydrophobic properties of the ceramic coated surface, most of the contaminants including dirt, bug stains and bird dropping are unable to penetrate the ceramic coated surface and hence making it easier to clean and maintain the surface.
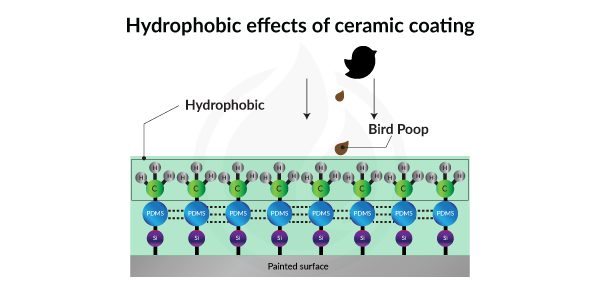
Additionally, PDMS is well-known for its chemical inertness and excellent thermal and UV resistance. The high degree of crosslinking density contributes to its chemical resistance. Ceramic coatings, in particular the ceramic coatings in the ecocoat series, are formulated to resist strong acids, caustic and also solvents like petrol and diesel. In addition, ceramic coatings help to prevent color fading caused by UV rays, which degrade the pigment in painted surfaces like cars and buildings.
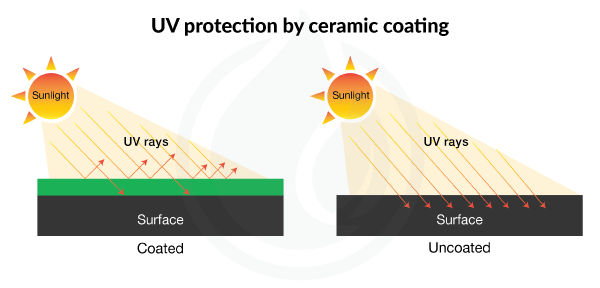
All ceramic coatings have designed with specific characteristics such as hardness, hydrophobicity and durability. Depending on the formulation of each individual coating and the purpose that it is created for, each coating will display different levels of common characteristics. For example, ecocoat KENZO is a specialized formulation with a 10H (pencil scale) hardness. Its key characteristics are 120° water contact angle, with silky like gloss and an extended durability period. ecocoat wheel however is designed for high heat resistance, increased durability and hardness.
To learn more about the eco-friendly coatings produced, formulated and manufactured by IGL Coatings, visit www.iglcoatings.com for more information. You can also email us at marketing@iglcoatings.com for further requests and articles.